Presses, from the ancient printing press to modern hydraulic behemoths, represent a cornerstone of manufacturing and industrial processes. This exploration delves into the diverse world of presses, examining their types, operation, applications across various industries, and the exciting future of press technology. We’ll uncover the engineering principles behind their design and discuss crucial safety considerations.
This in-depth analysis will cover a wide range of press types, from simple mechanical presses to sophisticated computer-controlled hydraulic systems. We will explore their applications in diverse sectors, highlighting how advancements in press technology continue to drive innovation and efficiency across industries.
Types of Presses
Presses are essential machines across numerous industries, each designed for specific applications. Categorizing them by function provides a clearer understanding of their capabilities and limitations. This section details various press types, highlighting their key features, applications, and comparative advantages and disadvantages.
Categorization of Presses by Function
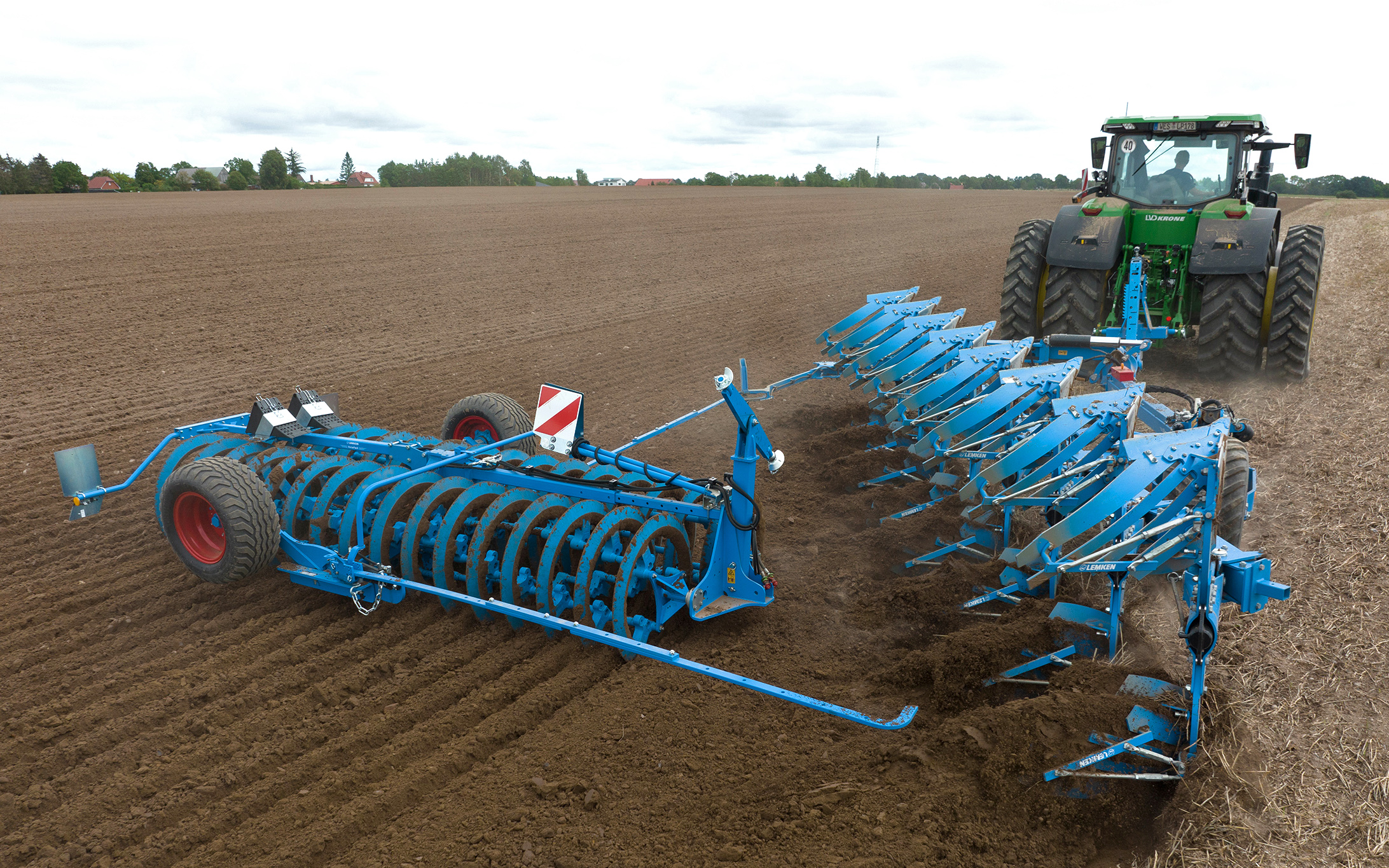
Source: agriland.ie
Presses can be broadly categorized into printing presses, hydraulic presses, mechanical presses, and others based on their primary function and mechanism. Each type possesses unique characteristics that determine its suitability for different tasks.
Specific Press Types, Features, and Applications
Type | Function | Key Features | Applications |
---|---|---|---|
Hydraulic Press | Forming, pressing, bending | High force capacity, precise control, versatility | Metal forming, forging, powder metallurgy, plastic molding |
Mechanical Press | Stamping, punching, forming | High speed, repetitive operations, cost-effective for high-volume production | Sheet metal fabrication, coin production, automotive parts manufacturing |
Printing Press | Image reproduction onto various substrates | High-speed printing, precise color reproduction, various printing methods (offset, flexographic, etc.) | Book printing, packaging printing, newspaper printing |
Screw Press | Compressing materials | Simple design, reliable operation, suitable for smaller-scale applications | Waste compaction, oilseed pressing, briquette making |
Comparison of Three Press Types
Comparing hydraulic, mechanical, and screw presses reveals distinct advantages and disadvantages. Hydraulic presses offer high force and precision but can be slower and more complex. Mechanical presses excel in high-speed, repetitive tasks but may lack the versatility of hydraulic presses. Screw presses are simple and reliable but are limited in force capacity and precision.
Press Operation and Maintenance
Safe and efficient press operation requires a thorough understanding of the equipment and adherence to safety protocols. Regular maintenance is crucial for extending the lifespan and ensuring reliable performance of the press.
Operating a Hydraulic Press
- Inspect the press for any damage or leaks before operation.
- Ensure the workpiece is securely positioned.
- Activate the press using the designated controls, gradually increasing pressure.
- Monitor the pressure gauge during operation.
- Once the operation is complete, release the pressure slowly and remove the workpiece.
- Clean the press and surrounding area.
Press Maintenance Best Practices
- Regular lubrication of moving parts.
- Inspection of hydraulic fluid levels and condition.
- Checking for wear and tear on components.
- Cleaning and removing debris.
- Periodic calibration of pressure gauges.
Safety Hazards and Preventative Measures
Potential hazards associated with press operation include crushing injuries, electrical shocks, and hydraulic fluid leaks. Preventative measures include using appropriate safety guards, lockout/tagout procedures, regular inspections, and employee training.
Preventative Maintenance Schedule for an Industrial Press, Presses
Inspection Item | Interval | Action |
---|---|---|
Hydraulic fluid level | Daily | Check and top off as needed |
Hydraulic system leaks | Weekly | Inspect for leaks and repair as needed |
Moving parts lubrication | Monthly | Lubricate all moving parts |
Overall press inspection | Quarterly | Thorough inspection for wear and tear |
Press Applications Across Industries
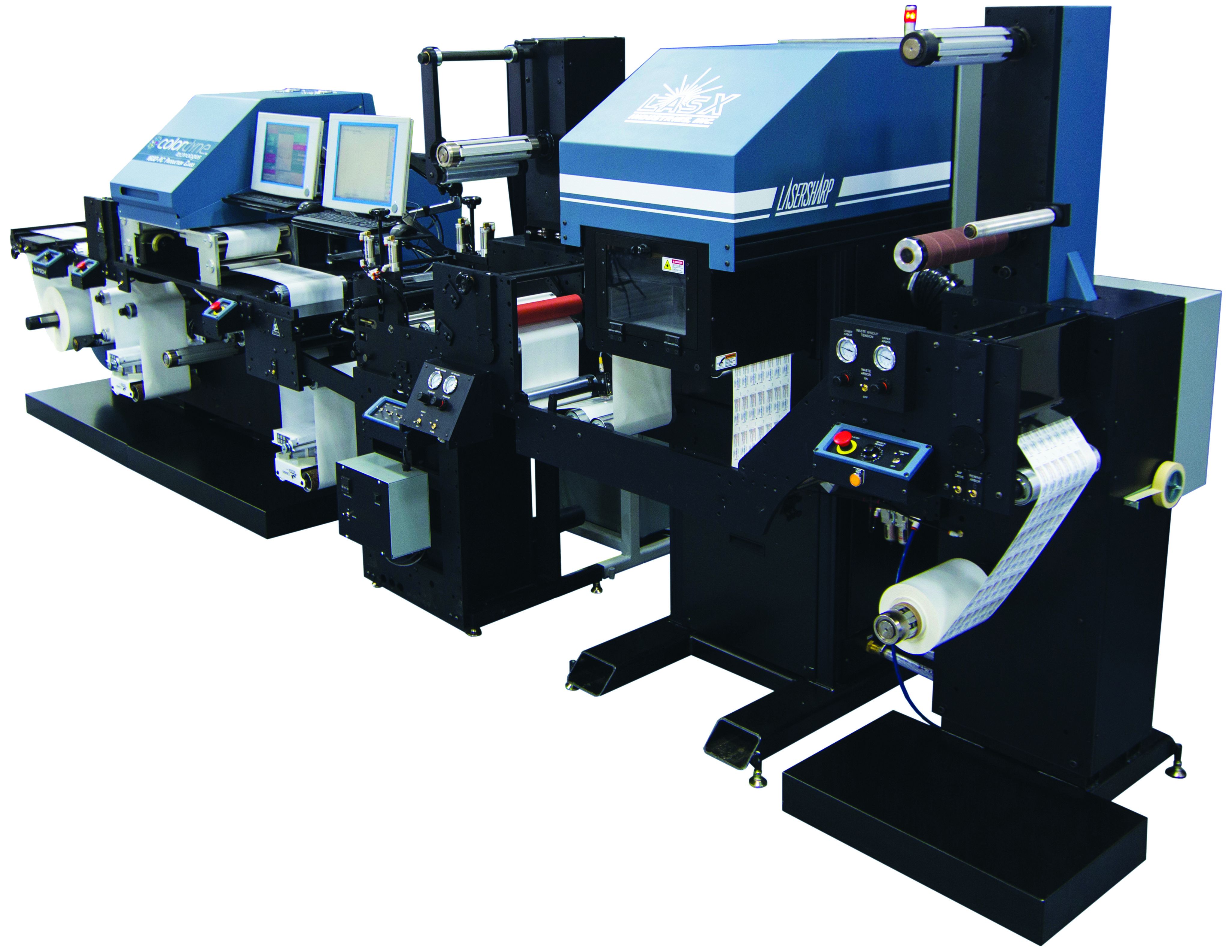
Source: labelsandlabeling.com
Presses are indispensable tools in diverse manufacturing sectors, demonstrating their adaptability and versatility across different production scales. This section highlights their application in various industries and the evolution of press technology to meet modern manufacturing demands.
Press Applications by Industry
- Automotive: Stamping of body panels, forging of engine components, pressing of various parts.
- Aerospace: Forming of aircraft parts, pressing of composite materials, production of specialized components.
- Electronics: Manufacturing of printed circuit boards, assembling electronic components, pressing of connectors.
Evolution of Press Technology
Press technology has evolved significantly, incorporating advanced materials, computer controls, and automation. Modern presses offer higher precision, speed, and efficiency compared to their predecessors. The integration of CAD/CAM systems allows for precise design and manufacturing of press components and tooling.
Presses in Different Production Scales
Presses are used across various production scales, from small-scale workshops utilizing simpler mechanical presses to large-scale factories employing sophisticated automated hydraulic and mechanical presses. The choice of press type depends on production volume, part complexity, and budget.
Press Design and Engineering Principles: Presses
The design of presses involves a complex interplay of engineering principles, material science, and manufacturing considerations. Understanding these principles is crucial for creating efficient, safe, and reliable press systems. This section delves into the fundamental engineering aspects of press design.
Fundamental Engineering Principles
Press design hinges on principles of mechanics, hydraulics, and materials science. Factors such as material strength, pressure distribution, and force transmission are critical considerations. Finite element analysis (FEA) is often employed to simulate stress and strain distribution within the press components, ensuring structural integrity and optimal performance.
Influence of Material Strength, Pressure, and Force
The selection of materials for press components depends on the required strength, stiffness, and resistance to wear and tear. Accurate calculation of pressure and force is essential to ensure the press can handle the intended workload without failure. Safety factors are incorporated into the design to account for unexpected loads and variations in operating conditions.
Role of Computer-Aided Design (CAD)
CAD software plays a vital role in modern press engineering, enabling the creation of detailed 3D models, simulation of press operation, and optimization of design parameters. CAD allows for efficient collaboration between engineers, designers, and manufacturers, streamlining the development process.
Diagram of a Hydraulic Press
A typical hydraulic press comprises a hydraulic cylinder, a piston, a ram, a worktable, and a control system. The hydraulic cylinder contains hydraulic fluid, which is pressurized by a pump to move the piston. The piston’s movement is transferred to the ram, which applies force to the workpiece placed on the worktable. The control system regulates the pressure and speed of the ram, allowing for precise control over the pressing operation.
Safety features such as emergency stops and pressure relief valves are integrated into the design to enhance safety.
The Future of Press Technology
Press technology continues to evolve, driven by the demand for higher precision, efficiency, and automation. This section explores emerging trends and potential future applications of press technology.
Emerging Trends and Advancements
- Increased automation and integration of robotics.
- Development of advanced materials for improved durability and performance.
- Adoption of digital twins and predictive maintenance technologies.
- Integration of advanced sensors and data analytics for real-time monitoring and optimization.
Future Applications
Future applications of presses may extend into new industries and processes, such as additive manufacturing, bioprinting, and advanced materials processing. Innovative designs incorporating flexible tooling and adaptable force profiles may enable the production of highly customized parts and components.
Recent advancements in printing presses are revolutionizing the publishing industry, impacting everything from newspaper production to personalized marketing materials. This increased efficiency is mirrored in other sectors, such as the innovative health initiatives detailed on the worldofwellpath website. The speed and precision of modern presses ultimately contribute to the rapid dissemination of information, a key factor in the success of public health campaigns like those highlighted by the site.
Therefore, the future of presses is inextricably linked to the efficient spread of vital information.
Innovative Press Designs and Functionalities
Examples of innovative press designs include servo-hydraulic presses offering precise control and energy efficiency, and presses incorporating adaptive control systems for real-time adjustment of pressing parameters. The development of advanced materials such as high-strength composites allows for the creation of lighter and more powerful presses.
Improved Efficiency, Safety, and Precision
Technological advancements are significantly improving press efficiency, safety, and precision. Automated systems reduce manual intervention, minimizing the risk of accidents. Advanced sensors and control systems enable precise control of pressing parameters, leading to improved product quality and reduced waste. Predictive maintenance reduces downtime and enhances overall operational efficiency.
Epilogue
The world of presses is dynamic, constantly evolving to meet the demands of modern manufacturing. From the fundamental engineering principles governing their design to the innovative applications shaping the future of various industries, presses remain essential tools driving technological progress. Understanding their operation, maintenance, and safety protocols is crucial for efficient and safe industrial practices.